At Elitewheels, our goal is to lead the way in the development of carbon wheels. For this reason, we incorporate the latest tech in our wheels in order to give riders the very best. While having the best tech can be nice, we seek to offer the best in quality control, customer service, and reliability. Since we design and produce our own resin, carbon fiber prepreg, rims, hubs, and wheels, we have unmatched control over the the quality of our wheels.
Let’s look into what make the Drive Helix wheelsets the next generation of carbon road wheels.

The Hub
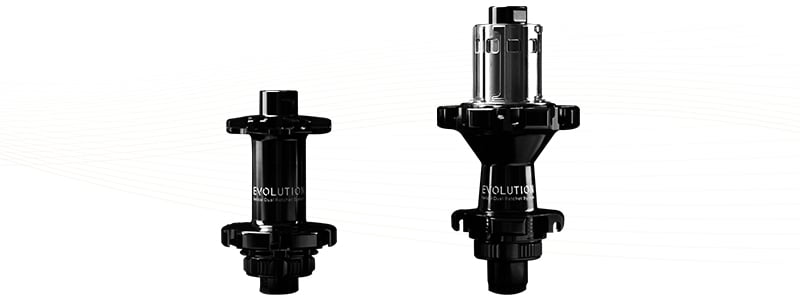
The biggest standout feature of the Drive Helix wheels is our new Evolution Hub. In designing it, the goal was to push the boundaries of what a hub could be. Instead of sticking with something traditional, our engineers thought of how the best hub of today could be improved upon. It has taken years from when then the initial prototype was designed until the final version was ready. Nothing worth having is easy. Let’s see what makes the Evolution hub an “evolution” in hub tech.
A New System
The most important feature of the hub is the Helical Dual Ratchet System. It uses two separate ratchet mechanisms and a helical ring drive to accomplish four things: to reduce rolling resistance, to increase engagement, to increase longevity, and to eliminate skipping and slipping. To understand how it works, let’s first look at the two separate ratchet mechanisms.
Common Bike Hub Types
There are many types of bike wheel hubs. The two most notable and common are pawl and ratchet and star ratchets. While there are other options, they have significant drawbacks for high-end road wheels, for example increased weight.
Pawl and Ratchet Hubs
Pawl and ratchet hubs are excellent for their potential for high engagement such as in our Gnar MTB wheels, their ubiquity, and their relatively lower manufacturing cost. They are tried and tested and used in some of the best road wheels. Our sponsored UCI Continental pro teams all use our Drive wheels with pawl and ratchet hubs.
Star Ratchet Hubs
The other main kind of hub is the star ratchet hub. This kind of freehub mechanism uses a single star ratchet mechanism that have all teeth engaged at once. This kind of hub is easy to service, and has all contact points transferring torque at once. This kind of hub is featured on our Velo TT Disc, Velo Six Disc, Drive Six, and other MTB wheels.
Potential Issues with Current Designs
While both pawl and ratchet and star ratchet designs are great and are raced at the highest level, they have few things that could be improved upon. For pawl and ratchet hubs, they have many small parts that makes it more difficult to service. Over time, some springs may weaken, and grease can thicken, leading to “nothing happening when pedaling.” Since the pawls are constantly in contact, they and the teeth of the ratchet can be prone to wear. Star ratchet hubs require springs to force the ratchet plates together. There is also potential for wear as the two surfaces are always in contact. They are have limited engagement.
The Evolution Hub
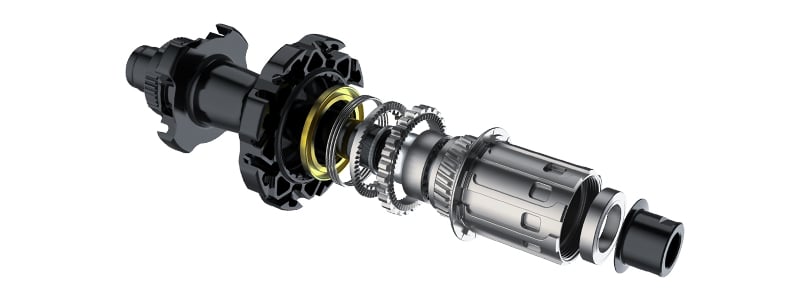
Engagement

While pawl and ratchet and star ratchet hubs have their strengths and weaknesses, the goal in designing the Evolution hub was to keep the benefits while eliminating the drawbacks. Our new freehub mechanism uses two ratchets instead of one. This significantly increases engagement to only 3° or 120 points of engagement, making it higher than any other traditional star ratchet freehub mechanism. It is now as high as some of the top pawl and ratchets.
Longevity
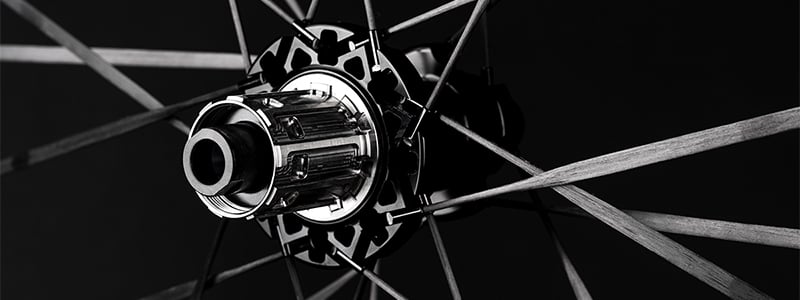
The Evolution hubs have significantly longer lifespans due to not only the titanium freehub body, which is strong and light, as opposed to aluminum and steel freehub bodies, but also due to the internals. Instead of using a powerful spring to force the ratchet plates together, this is accomplished using rider torque, allowing for a weaker spring, reducing wear. In addition, there are two offset ratchets rather than one, reducing wear even further.
Besides the freehub body and the Helical Dual Ratchet System, the Evolution hubs also feature TPI ceramic bearings. These have tighter tolerances and are made out of stronger materials, meaning there will be less wear than some other competing ceramic and steel bearings.
Rolling Resistance
One of the side benefits of not needing such a strong spring like with traditional ratchets, is that there is less rolling resistance. When freewheeling, the wheel can spin far longer, saving you precious watts.
In addition to the advantages of our new Helical Dual Ratchet System, the hubs feature TPI ceramic bearings, which roll smoother and longer due to not just the bearings themselves, but also because we precisely machine our own hubs using FANUC CNC machines with just 0.02mm of tolerance. This means the bearing seats are round enough to support the best ceramic bearings, allowing them to last and to experience low rolling resistance.
The Rims
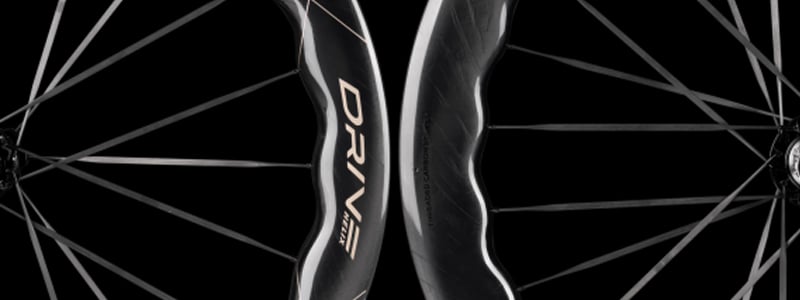
What makes the rims of the Drive Helix wheels unique is not just their undulating design based on the Tubercle Effect found in nature, but also the careful choice of internal and external rim widths based on the rim depth. Each wheelset also has a different front and rear wheel rim depth. Below we will compare more traditional aero carbon rims to the Drive Helix carbon rims.
Traditional Aero Carbon Rims
What makes carbon wheels attractive are the properties of the material itself. It has a very high strength to weight ratio, does not experience fatigue like alloy alternatives, and can be molded into more complex shapes. Most carbon wheels feature a round design that is uniform. More U-shaped rims are better for crosswind stability, while more V-shaped rims are better for aerodynamics in ideal conditions. While these wheels are great, they tend to either be one or the other.
Drive Road Rims
In order to offer a balance of aerodynamics and crosswind stability at 0-15% yaw angles, the Drive road wheels we have offered for over the past two years have had a U/V-shape. These are the wheels of choice of our six sponsored UCI Continental pro teams and have performed well in some of the most competitive events, helping riders to win stages and races in Europe and Asia.
We offer three different rim depth options for both disc brake and rim brake riders. The Drive 40D and 40V are best suited for climbing. They are not as aerodynamic, but they perform well in crosswinds, climbs, and sprints. They have very low inertia, making them fun to ride. The Drive 50D and 50V are excellent all-round wheels that are good for most riding conditions, they are still light at 1300 grams while being more aerodynamic. They are more affected by crosswinds when compared to our 40mm wheelsets. The Drive 65D and 65V are the most aero, but they are more difficult to control in crosswinds and do not climb as well due to their heavier weight, due to the extra carbon fiber needed to make them.
Drive Helix Rims
At Elitewheels, one of our missions is to offer something for all riders. We realize that the needs and preferences of cyclists are not all the same. For this reason, we sought to create something that would satisfy the needs of riders who would like more control and stability without sacrificing aerodynamics and weight. The Drive Helix rims are also wider to accommodate wider tires, which can provide more comfort. Let’s look at the tech behind the Drive Helix rims.
UNI Carbon Fiber
What makes our Drive and Drive Helix wheels unique is that they use our in-house carbon fiber prepreg, the individual sheets of carbon fiber mixed with resin that are used to make carbon rims. What makes our UNI carbon fiber different is that is not only features our custom resin that we design and produce ourselves, but also genuine Japanese Toray carbon fiber, which has a stronger strength to weight ration as compared to cheaper Chinese and Taiwanese carbon fiber.
Undulating Rim Profiles
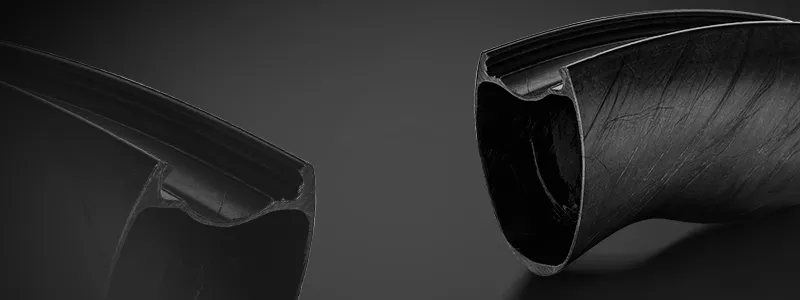
The most striking feature of the Drive Helix wheels is the undulating or wavy rims. They are just as much about function as they are about form. This rim shape is based on the Tubercle Effect which exists widely in nature. What it means for rims is that they allow for additional stability when there is a pressure differential between one side of the rim and the other. A difference in pressure can cause instability, especially with deeper rims.
The wavy profile coupled with our U/V-shaped rims allows for exceptional crosswind stability. This is very noticeable not only in windy conditions, changing directions at high speeds such as during a descent, and when cycling near large vehicles.
Mixed Rim Depths
While most wheels have a single front and rear rim depth, many riders including professionals prefer mixed rim depths due to their multitude of benefits. Riders will choose a shallower front wheel and a deeper rear wheel. The shallower front wheel will be easier to control in the same ways as mentioned above. A shallow depth wheel is also lighter. The deeper section rear wheel is more aerodynamic. This gives a balance of lightweight, aerodynamics, and crosswind stability.
With the Drive Helix wheelsets, this mixed depth comes as standard. The specific depths were chosen especially for certain riding conditions. There are three disc brake models, the Drive Helix 46D, 57D, and 68D. Each of them has a different set of rim depths whether you prefer climbing and descending, all-round riding, or going fast on the flats.
Disc Brake Models
As mentioned above, there are different wheel models. The first is the Drive Helix 46D. This wheelset is the lightest option, making it perfect for the climbs and getting the KOM. It has been designed to have low inertia making it the best choice for those who want an agile wheelset that can accelerate quickly.
The next is the Drive Helix 57D. This wheels is perfect for those who ride a bit of everything. It is light but also aerodynamic, making it ideal for most conditions. This rim depth is favored by our pro riders on most stages.
The final option is the Drive Helix 68D. This wheelset is designed to be best at riding on the flats with the occasional hills. It is much more crosswind resistant than other deep section wheels, making is perfect for those who like to get in a more aerodynamic position. You will notice a big difference in stability compared to other wheels with similar depths.
Rim Brake Options
We believe that riders should have the choice in when it comes to what kind of bike they want to ride. Because of this, we not only offer disc brake wheels, but also rim brake ones. After the release of our disc brake Drive Helix wheels, we will offer the Drive Helix 46V and Drive Helix 57V.
Internal and External Widths

One of the most important but overlooked things when it comes to improving the aerodynamics of a wheel is actually the tire! While our Drive road wheels were aerodynamically optimized for 25-26mm tires, the Drive Helix disc brake wheels are designed for 28-30mm tires. This means increased comfort for our sponsored teams as well as the amateur riders who use our wheels. The internal rim widths are 21mm, making them perfect for wider tires. The front external rim widths are 1mm wider than the rear external rim widths. This additional outer rim width on the front wheel improves its crosswind stability, allowing cyclist to ride with more assurance and control.
Reduced Hook Design
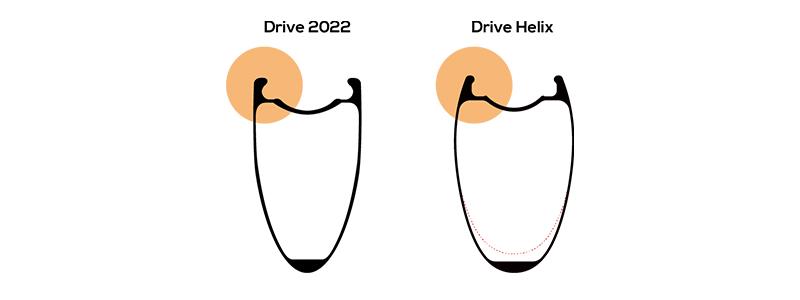
Another way in which the new Drive Helix wheels is leading the pack in the reduced hook design. It takes the from the advantages of both hookless and hooked designs. Hooked rims are tried and tested and work with a host of different tires. Hookless rims have aero benefits, but are limited by tire choice and have strict pressure limits that are often too low for narrower road bike tires in order for them to be safe. Our reduced hooks allow for high tire pressures to be used without any additional risks. In addition, our new hook design allows for the tire and rim to have a much more seamless transition, reducing drag.
Spokes
Just like the hub and rims, we have put significant consideration the spokes. They are an integral part of a wheel, and we are making use of arguably the best spokes available today on any road bike. Lets take a look at our new carbon spokes and how they compare to steel spokes as well as the ones in our popular Drive road wheels and the Drive G45 CS.
Steel Vs Carbon Spokes
Steel spokes have been the only option for bike wheels for well over a century. Later, some wheels began incorporating carbon spokes. While both have their benefits and drawbacks, there are a few things to note. Steel and carbon spokes both work very well. They are both now tried and tested.
Carbon spokes have the benefit of being able to be molded into more aerodynamic shapes. They are also 7% stiffer and also do not fatigue. This often comes at a price, as carbon spokes and the wheels that use them are more expensive to produce. Lets look at what kind of carbon spokes are available and how they have changed over time.
One of the most common questions about carbon spokes is about their durability. The spokes that we use and steel spokes can withstand roughly 40 joules of side or front impact force depending on spoke tension, making them safe enough for even pro riding. They are so strong during riding that when we conduct our vertical impact tests to get the UCI certification as well as even more destructive tests more than doubling that force, the rim will fail far before the spokes. Carbon spokes are very safe and reliable regardless of what kind of road riding you do.
Not All Carbon Spokes Are Created Equal
In the past, all carbon spoked wheels were monocoque designs. What this means is that the spokes are bonded to to the hubs and rims. While this does have some advantages like not needing to true wheels, a single collision strong enough to brake a spoke meant that the wheel would no longer be usable. Not only is this expensive but also not environmentally friendly.
Things are changing now, and we have available some of the first replaceable spoke carbon wheelsets. They are just as easy to replace as traditional steel spokes while keeping the benefits of carbon fiber spokes. In case of a collision, we include extra spokes with every one of our Drive and Drive Helix wheelsets. In addition, we have a growing network of service centers just in case.
Drive Carbon Spokes
Our Drive spokes, as mentioned above, are fully replaceable. They are lightweight at roughly 3.3 grams each and have a bladed aero design, making them superior to bladed steel spokes. The weight is 30% less than Sapim CX-Ray steel spokes, which for a long time were considered the best racing spokes. Their threads also use anti-loosening tech to keep them securely in place.
Drive Helix Carbon Spokes
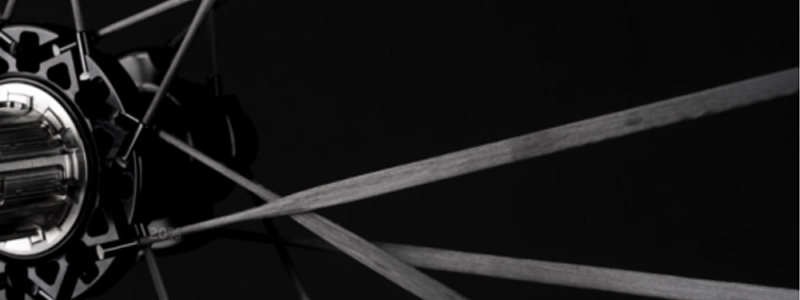
What separates the Drive Helix Spokes from the Drive spokes is not just that they are noticeable more aero, at 5.2mm instead of 3.2mm, but they also have a complete re-design that prevents them from twisting. They feature a special spoke head that prevents them from loosening to even a greater extent than Drive spokes.

After years of riding, Drive spokes may lose a slight amount of tension. This happens to all wheels. When building wheels, we actually stress relieve wheels a total of 16 times and re-true them twice. The spokes being fixed in place at the hub makes twisting impossible, even after years of riding. This had the added benefit of the spokes always being in the most aerodynamic position.
In addition, the spokes maintain their lightweight 3.3 gram construction, which adds up, saving more than 50 grams over a wheelset with lightweight steel spokes.
Bearings
Bearings, while often overlooked, are at the heart of the wheel. They can make or break a wheel. Poor quality bearings can not only have unfavorable high rolling resistance but can also have poor longevity, leading to worsening performance. At Elitewheels, we specifically choose the best bearings for the job.
Steel vs Ceramic Bearings
Steel bearings are commonplace in most wheelsets except for certain high end ones. They are also the bearing of choice for MTB wheels as they can handle extreme forces that are not encountered on road and gravel trails.
We choose to use mixed ceramic bearings because they can not only reduce rolling resistance, making wheels run more smoothly, but also for their longevity. The right ceramic bearing can last tens of thousands of kilometers with little to no change in rolling resistance.
In order for both steel and ceramic bearings to perform their best, the hub must be machined to the right tolerances. This precise machining prevents extra stress from damaging the bearings. A well machined bearing seat should be very round, so the bearing is not compressed.
Drive Bearings
Just like our other road and gravel offerings, Drive wheels feature mixed ceramic bearings. We choose S&S bearings due to their reliability and low rolling resistance. They deliver excellent performance and are used by our six sponsored UCI Continental pro teams. The hubs coupled with our ceramic bearings have extremely low rolling resistance, allowing them to spin much longer than other wheels.
Drive Helix Bearings

When making Drive Helix wheels, no expense was too great. We chose TPI bearings for their high precision. Our goal in designing the Drive Helix wheelsets was not just to create something fast, but also something that could last a long time with as little maintenance as possible. TPI bearings are manufactured with extremely high precision and with harder materials.
From the races to the bearings themselves, TPI bearings are designed to last longer than other ceramic bearings, which in the right conditions already last longer than steel bearings. TPI bearings are more resistant to contamination, making them the perfect bearing for any road bike wheel.
1 comment
Gideon London
These latest wheels the Drive Helix sound very interesting and I’m looking forward to riding and testing out your claims, which I hope will be all positive.
The article above talks about wastefulness and the environment, relating to Carbon specifically I guess. So my question. Thinking long term when parts do eventually wear/break, usually bearings, axils and free hub ratchets especially. As a consumer access to these spare parts is essential rather than disposing of a wheel. How long will you be planning on keeping spares for all these wheels? Realistically it should be for 10 years. Where on the website can we find spare parts that are available. Is this something you hope to develop in the future.
Thank you
Comments are closed.